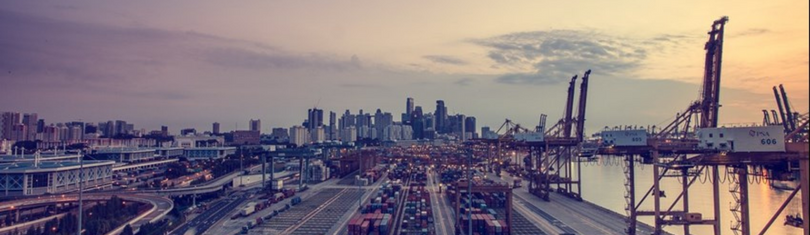
In today’s digital age, efficiency in and diligence of such processes are supported and driven by data. Once you decide to invest in a Product Lifecycle Management (PLM) solution, you will need to understand this critical role of data, knowing where the data comes from and what to do with it. Once you understand it, a software solution will automate most of the hard work, remove the effort, and reduce the time required. The result is a higher level of productivity because everything gets done faster.
WHAT IS PLM?
PLM is the process of managing the entire lifecycle of a product. ‘Entire’ means exactly what it says—from the moment the concept is born to production and, if required, through to its phasing out and recycling.
The entire product lifecycle
PLM connects business processes and systems
to optimize operational performance around lead times, cost and quality
Knowing what to do and what was done, when
A PLM system is the central repository of knowledge and information about a product. It is the hub where any actions undertaken—by any department—or as instigated by the intervention of any third party (such as component suppliers, packaging designers or other deliveries) are recorded.
Ensure your product information is always centralized, coordinated and controlled, available at the right place at the right time:
- At the level of quality that the company business requires
- Checked by the necessary role in the Product Delivery process
- Reusable for new and repeating projects
- Available for distributed teams and to your Supply Chain
- Reliable without exceptions and compromises
A PLM system ensures that no critical actions are overlooked through this continuous and transparent availability and resultant audit trail. Anybody involved in any aspect of the product’s life and evolution can understand the impacts of others’ actions that require a response regarding their own role. For example, when the purchasing department picks up an order from the PLM system, they can be confident knowing that all information is up to date.
This is the ‘people’ aspect of PLM, improving visibility to improve timely intervention and continuous focus. The system can be made available to the entire company, with relevant permissions set.
Keeping track
Examples of the actions (easily searchable within the system) over which the system provides complete visibility and traceability include:
- Products
- Product Change Management
- Quality Management
- New Product Introduction
- Design Reviews
- Compliance
- Aftermarket Processes
The benefits of PLM
The overarching value of PLM is ensuring that whoever needs to be aware of the product’s status at any given time is informed. It is also far more than an ‘archival’ solution. It is a unified means of control, consistently driving and enabling best practice management. When actions are required, its function is to present the latest information at all times.
The more rigorous your control over each phase of a product’s lifecycle, the more you will eliminate errors, accelerate design times, and serve customers not only more responsively but also more proactively:
- Reduced risk of errors with updated and automated data sharing
The role and value of data are pivotal in ensuring no oversight in a product’s lifecycle. By connecting product development with every part of the company's value chain, you can ensure that everyone in the company always has access to the correct and updated design data.
An integrated approach to data—bearing in mind that integration relates not just to inter-departmental connections but can also enable you to send and receive product information to ERP systems on-premise or in the cloud—makes it easier to find and reuse design and technical data. It provides suppliers access to product information and design changes during the tender round.
- Significant savings in design time
Many of a PLM system’s features allow designers to spend more time on the actual design work and innovation without getting caught up in or side-tracked by admin tasks.
Designers can enrich the model data with smart properties, such as dictionaries and calculated field values. The system can automatically create information needed outside the engineering department, such as bill of materials (BOM) and divisible files.
- Streamlined sales process
Through simple and rule-based configurations, which do not require an understanding of the technical context, you can streamline the sales process through a greater degree of customization, shorter delivery time and fewer errors.
- Better support and service offerings
By having sufficient knowledge of delivered equipment, you can link a service program to the system and create an understanding that necessary service and spare parts provide further business opportunities.
The design and manufacturing advantage
Design and manufacture any type of product. A PLM solution will help you manage the end-to-end process more efficiently, with greater control and earlier and more sustained collaboration.
Its predominant use is among companies in the industrial equipment, transportation and automotive, oil and gas, project engineering, and building component manufacturing sectors.
A company’s business model is more relevant than its sector when defining what is required from a PLM solution. The model may be of an Assembly to Order type (ATO), where products are assembled from components after the receipt of a customer order. It may be of an Engineer to Order type (ETO), where each customer order results in a unique set of part numbers, bills of material, and routings. These process variants will determine the parameters for your PLM system.
PLM is not just for large, complex companies
PLM solutions are ‘size-agnostic’. Process is process, after all. Improving it is a universal business goal. There are three fundamental questions to ask when creating the business case for a PLM solution within your own organization:
- Where are the pain points/improvement potential?
What is your current situation regarding challenges, bottlenecks, information sharing, audit trails, customer satisfaction, and speed to market?
- What are your short-term and long-term goals?
Are you looking for quick fixes or rapid resolutions to current issues? Do you foresee that an overhaul of your approach to product lifecycle management can have a profound effect across the business? Are you expanding, looking for new markets, seeking to serve customers better, or enhancing your competitive advantage?
- Do you seek change?
Are you prepared to change your current processes and workflows? Are you prepared to champion the organization and culture change that this might entail? Have you consulted with and gained feedback for the principal users and stakeholders within your business or even undertaken conversations with major customers about their expectations?
Are you looking to adhere to Lean principles to eliminate waste from processes and systems, streamline process flow, and improve quality across your whole product value chain?
Choose your solution
Answering these questions will enable you to create a clear and specified vision about your next step, moving the business—at the heart of your products and how you manage their lifecycles—from its current to its anticipated future of working.
The next step is to survey and assess your options regarding PLM solution partners who may not only provide the software but will also assist in advising how your business may customize, implement and integrate it, making it your tool to meet your needs and enhance the capabilities and motivation of your teams.
The PLM Return on Investment
PLM benefits in areas beyond CAD data management and collaboration through the product’s lifecycle. For this reason, we have discussed its value across the company culture and every department within the company.
You may not have thought, for example, that HR will feel the benefit, but the more you embrace an advanced, technology-driven, data-centric approach to how you work, the more you attract talent.
People like to work for forward-thinking businesses. They are enthusiastic about working with technology, collaborating with broader teams, and supporting management in its commitment to staying ahead of the field.
PLM delivers ROI benefits at every phase of the product’s lifecycle:
Sales: Ensuring that the correct products and parts are selected and sold
Procurement: Ensuring that the correct item revisions are ordered and documentation is provided to the supplier
Production: Confidence that the correct items are assembled and delivered and that engineering changes are implemented in a controlled way
Service and maintenance: Making sure that the correct spare part documents are created and information related to each individually delivered product is stored, managed and easily accessible at any time.
As Industry 4.0 and Smart Manufacturing develop, with a relentless pace of technological innovation, such as the Internet of Things (IoT), PLM is an asset which will align your business with partners, your supply chain, your customers and the expectations and needs of your stakeholders.
When connecting real-time information from an individual product—or fleet of product configuration data—managed in PLM, you can extensively expand the opportunities related to additional products and service sales to your existing customer base.
Please visit our website to learn more about the various PLM solutions we offer.