With the growing uncertainty in our economy, now is an important time to be looking at how accurately you can interpret the design information provided at tender.
The consequences of inaccurate takeoff will be greater now than ever.
Recent reports show depressed activity within the sector last month, after even steeper falls in July, meaning there are already fewer projects out there to be won as clients begin to put plans on hold.
Inflation is increasing rapidly in many countries and construction companies will feel the effects of this also. As well as increased costs in materials and labor, supply chain pressures and shortages may well compound this.
Rising fuel prices in turn push up costs across the board; from staff travel to material delivery and even running the plant on site itself. All will have a significant affect.
In short, the already tight margins of our industry stand to be pushed to the limit in the near future. Uncertainty of future costs is complicating the bidding process and if the quantities identified as part of this process are incorrect, then the impact may be significant; either winning projects through omissions or losing them by overestimating.
Whilst those future cost predictions will need to be assessed and estimated using historical data, economic insight and the actual quantities behind them should be easier to identify.
Using a product like Autodesk’s Takeoff, estimators are able to utilize the power of the cloud to access quantities from the models.
As part of the Autodesk Construction Cloud suite of products, Autodesk Takeoff combines 2D and 3D estimating in one solution. Using a single source of truth, in this case Autodesk Docs where the files are hosted, allows seamless access for the whole estimating team and ensures everybody is working to the latest information.
Within the system is the ability to classify takeoff items and these can be aligned with standards like Uniclass or NRM as well as your own customized system.
Takeoffs are split into packages within the system and these can be configured and reused across all your projects, saving time and helping to standardize the process. It is also possible to reuse measures for multiple elements and to set up calculated totals; for example, a single measure for the area of a room can build up line items for the square meterage of carpet, be reused for the underlay but may also calculate a volume of screed by adding a depth into the calculated field.
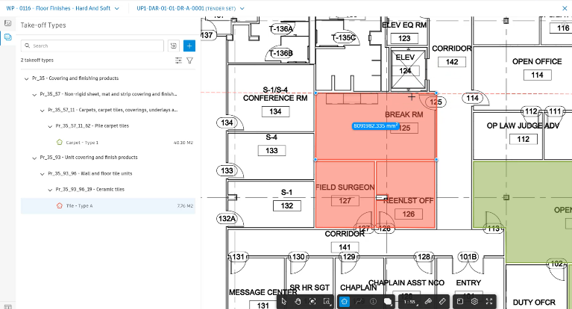
Takeoff directly from the 3D adds another level of automation, allowing use of the data within the model to help categorize all elements.
The combination of both 2D and 3D in the same solution helps to ensure there are no oversights in the takeoffs. What may not be clear or visible in 2D can be clarified by checking the 3D views, improving accuracy and eliminating potential scope gaps.
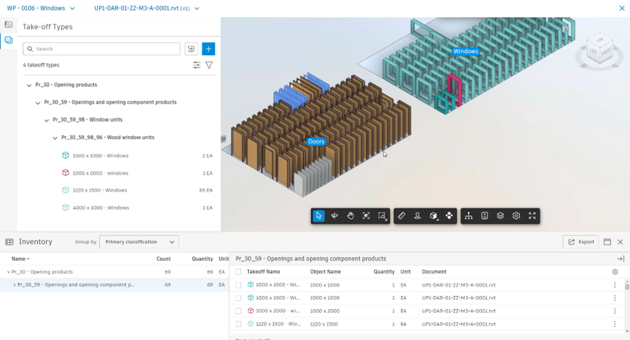
Finally, all the data you build up is scheduled automatically, can be organized as you need and exported.
All of this will go towards producing the most accurate estimates possible, making them more competitive and faster to produce, a must in the current climate.