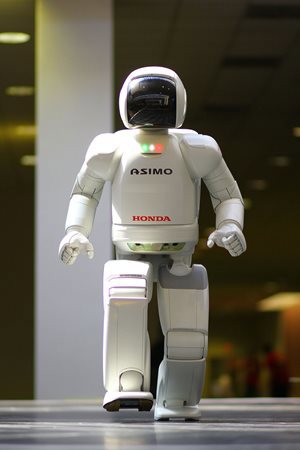
Robots in the manufacturing arena have been with us since the late 1950s and have evolved in other areas such as logistics, where they are often the norm. We even have robot domestic appliances available as consumer products.
One of the key applications of a robot is to automate repeatable activities, in a consistent, controlled, safe manner. Often these may have been mundane tasks previously completed by humans or tasks that could be difficult or unsafe for humans to perform.
In recent times that same automation has been applied to virtual robots performing software functions. We have bots that index the Internet, customer service bots, Autodesk AVA for example, and also more malicious bots such as spam generators and password crackers.
In Inventor we have our own bot, iLogic, which, with a little configuration and instruction, can be used to do our bidding, taking away the mundane tasks and allowing us to focus on tasks and developing products that make better use of our skills and intelligence.
So, what exactly can we use iLogic for? Well the simple answer to that is a great deal, so in this blog post we will give you a brief overview of the different aspects we can automate and control.
Process automation and design control
In iLogic our instructions take the form of rules. iLogic rules can be specific to models, or they can be external rules which can be applied to any Inventor file. Our internal model specific rules will trigger automatically when a related parameter changes. We can also trigger rules, including external rules, by intercepting other events such as opening and saving files.
We can easily break down our rules to those that relate to process automation rules, normally external rules, and design automation rules, internal and specific to the design model.
Process automation includes automating the production of documents and data for downstream processes or importing information from upstream. For example, if every sheet metal part requires a flat pattern dxf for our cnc production process, then we can use our iLogic robot to do that for us on every save with zero additional user input required.
Design automation rules allow us to change and adapt our models based on our design scenario. Our design rules can control which components are included in or excluded from our models, control the sizes and features in those models and set model limits. We can add rules for controlling the associated information such as material and appearance.
iLogic gives us a fully configurable interface to make it simple to interact and trigger our design rules and produce the required model.
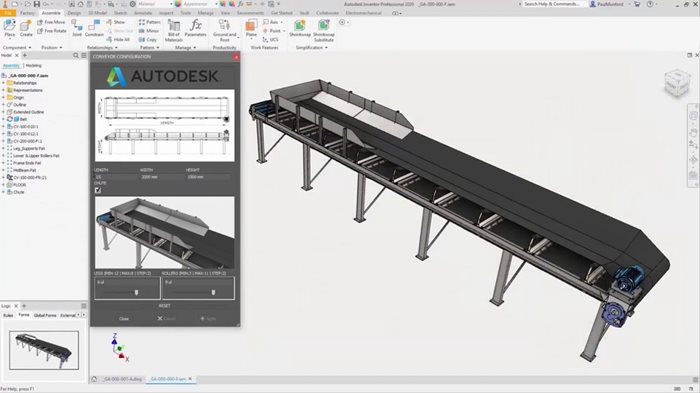
The iLogic rules we can add, use and trigger, can be simple functions to replace one simple task, or can include a multitude of functionality up to a highly specific and functional customized configuration environment.
There is no limit to the rules we can add, as far as number or complexity, and as iLogic can also access the Inventor api, along with any other .net based library, the possibilities are limitless.
The Advantages of iLogic
The obvious advantage when applying iLogic to our design environment is to reduce the time required to produce the information we need. That can translate simply as a cost saving, but that is not the only advantage. Reducing the time required may lead to faster turnaround, for example, on pre-sales information required for accurate quoting. This can lead to an increase in sales revenue as well as reducing the cost required for processing those sales. Also, with automation, the level of expertise required to carry out the necessary tasks can be reduced, enabling skilled resource to be better utilized.
iLogic allows us to capture the knowledge about how our designs are driven, lowering reliance on information being ‘known’ or having been imparted to others. A model with the configuration rules captured ensures that only designs that can be manufactured are able to be generated. As well as ensuring conformity of design this can also allow the configuration models to be used by others, such as the sales team or online, safe in the knowledge that valid options will be chosen.
Another advantage of implementing rules, for processes or design, is that consistency can be ensured. Typically, therefore, you would expect an increase in quality with a reduction in human error in the process. However, as with any robot, it is only as good as the instructions input so incorrect instructions will result in incorrect designs, though they will be consistently incorrect.
What next?
So, in summary we can use iLogic to automate repetitive Inventor tasks, making our engineers more effective and more efficient, reducing those tasks to minutes not hours.
At Symetri we offer a number of services to help you take advantage of iLogic in automating your design processes. From training your users, in the classroom or virtually, to implementing configurators for sales and production.
We have recently introduced a new service to the Symetri portfolio – iLogic Agile development workshops, which is a great way to get up and running quickly with iLogic automation benefits.
Houdini is just one of our customers who are taking advantage of iLogic, with our assistance. Find out more here.
For an executive overview of iLogic from Autodesk take a look at this video.